Thermal imaging, also known as infrared thermography, is a non-invasive diagnostic technique that uses infrared cameras to detect heat patterns in electrical systems. This advanced method allows maintenance teams to identify overheating components, loose connections, and overloaded circuits without shutting down equipment.
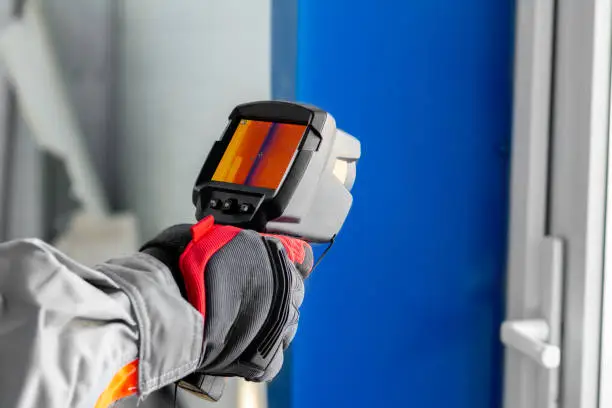
Thermal imaging visualises heat emissions and helps pinpoint potential problems that could lead to costly failures or safety hazards. This technique improves system reliability and safety, offering a proactive approach to maintenance that reduces risks and downtime. It is a vital tool for modern electrical system management.
For comprehensive assessments, consider electrical thermal imaging services to identify hidden issues and ensure the safety of your electrical systems.
Key Applications Of Thermal Imaging In Electrical Systems
One of the most important applications of thermal imaging in electrical systems is detecting overheating components. Various issues, including poor connections, overloaded circuits, or failing components, typically cause overheating. Below are some of the specific problems that thermal imaging can help identify:
Detecting Overheating Components
Overheating components can be a precursor to electrical failure, fires, or significant damage to equipment. Thermal imaging allows for the early detection of temperature anomalies that may not be noticeable during a routine inspection.
Identifying overheating areas before they reach dangerous levels is critical for maintaining system integrity.
Identifying Loose Or Corroded Connections
Electrical connections that are loose, corroded, or otherwise compromised increase electrical resistance. This heightened resistance generates excessive heat, resulting in more severe damage or even electrical fires if not addressed in time.
Thermal imaging is invaluable for detecting these problem areas, as loose or corroded connections will appear as localised hot spots on infrared images.
In traditional inspections, detecting such faults might involve shutdowns or disassembling equipment, but technicians can spot these problems without interrupting the system’s operation with thermal imaging.
Spotting Overloaded Circuits
Overloaded circuits are a major cause of overheating in electrical systems. When circuits carry more current than they are designed for, the excess energy generates heat, potentially damaging components and increasing the risk of fires.
Thermal imaging helps technicians identify areas where temperatures exceed safe limits, enabling them to address the issue before it escalates. This could mean redistributing the load or upgrading the circuit to ensure it can handle the required capacity.
Detecting Imbalanced Loads In Three-Phase Systems
Load imbalances in three-phase electrical systems can lead to localised overheating in specific parts. Thermal imaging is an effective way to identify these imbalances, as it highlights areas with higher-than-usual temperatures.
Technicians can then redistribute the load to ensure even power distribution, preventing excessive heating and reducing the risk of system failure.
Identifying Failing Electrical Components
Electrical components such as transformers, circuit breakers, and switches can fail due to age, wear, or poor design. Over time, even small faults in components can lead to major failures if left unchecked.
Thermal imaging enables maintenance teams to detect early signs of malfunction, such as unusual temperature variations or localised hot spots. Identifying these issues early can extend the lifespan of equipment, prevent unexpected downtime, and avoid costly repairs.
Benefits Of Thermal Imaging In Electrical Systems
Thermal imaging offers several significant advantages for maintaining and managing electrical systems. Regular use of this technology enhances system safety and reliability and improves overall operational efficiency.
Reducing Unplanned Downtime
Unplanned downtime can be incredibly costly, particularly in industries where continuous operation is critical. By incorporating thermal imaging into routine maintenance schedules, companies can detect and address problems early before they cause unplanned system failures.
This proactive approach helps minimise disruptions and ensures that production processes continue smoothly.
Extending Equipment Lifespan
One key benefit of thermal imaging is that it helps identify issues that may go unnoticed, such as overheating or resistance buildup in electrical components. By addressing these problems early, businesses can extend the life of their equipment, reduce the frequency of replacements, and lower long-term maintenance costs.
Enhancing System Reliability
Thermal imaging provides technicians with a detailed overview of the health of the entire electrical system. Businesses can continuously monitor temperature trends and identify weak points to ensure their systems run efficiently and reliably.
This helps reduce the risk of accidents or breakdowns and ensures that safety standards are met across the organisation.
Incorporating Thermal Imaging Into Maintenance Programs
Businesses should integrate thermal imaging into their preventive maintenance programs to fully harness the benefits of thermal imaging. Regular inspections, documentation, and trend analysis are key to maximising the effectiveness of this technology. Below are some steps to consider when developing a thermal imaging schedule:
Establishing Regular Inspection Intervals
The frequency of thermal imaging inspections should be based on the equipment’s criticality and the environment in which it operates. Mission-critical systems or those in harsh operating environments may require more frequent checks.
For other systems, inspections might be scheduled annually or biannually, depending on their importance and the potential risk of failure.
Prioritising Critical Systems And Components
Not all electrical systems and components are equally important. When creating a thermal imaging schedule, it’s crucial to prioritise critical equipment, such as transformers, circuit breakers, and high-load panels.
These components are more likely to experience faults and, if left unchecked, may lead to more severe system failures. Focusing thermal imaging inspections on these areas helps address potential issues promptly.
Documenting Findings And Analysing Trends
Documenting the findings from thermal imaging inspections is essential for identifying trends. By tracking temperature variations and noting areas where problems have occurred, maintenance teams can predict when certain components may need repairs or replacement.
This data-driven approach enables more informed decisions and better resource allocation in the maintenance process.
Conclusion
Thermal imaging is an invaluable tool for proactive electrical system maintenance. Detecting overheating components, loose connections, and other potential issues early helps prevent costly failures, reduce downtime, and extend the lifespan of equipment.
This non-invasive technology enables inspections without disrupting operations, enhancing system reliability and safety.
Integrating thermal imaging into routine maintenance schedules allows businesses to address problems before they escalate, ensuring smoother, safer, and more efficient electrical system operations for the long term.
Frequently Asked Questions
What Are The Main Advantages Of Using Thermal Imaging In Electrical Systems?
Thermal imaging offers several key advantages, including detecting issues like overheating, loose connections, and overloaded circuits without shutting down equipment.
This non-invasive method allows for continuous monitoring, preventing unexpected downtime and extending the lifespan of electrical components. It enhances safety by identifying potential hazards early, helping companies avoid costly repairs and accidents.
How Often Should Thermal Imaging Inspections Be Conducted?
The frequency of thermal imaging inspections depends on the criticality of the electrical system and the operating environment. High-risk or mission-critical systems may require more frequent inspections, such as quarterly or biannually, while less critical systems could be checked annually.
Establishing a regular schedule based on system importance helps ensure the timely detection of potential issues.
Can Thermal Imaging Detect All Types Of Electrical Problems?
While thermal imaging is highly effective for detecting overheating, loose connections, overloaded circuits, and failing components, it may not identify all types of electrical problems, such as those related to electrical insulation or internal faults that don’t generate heat.
It is best used with other diagnostic methods to ensure comprehensive health monitoring.