Any company serious about increasing profits and streamlining operations would do well to focus on lowering freight expenses. Companies need to come up with creative ways to cut costs without lowering the quality of their services to survive in this highly competitive industry.
Knowing how to reduce freight expenses can help any business, no matter how big or little, save a ton of money.
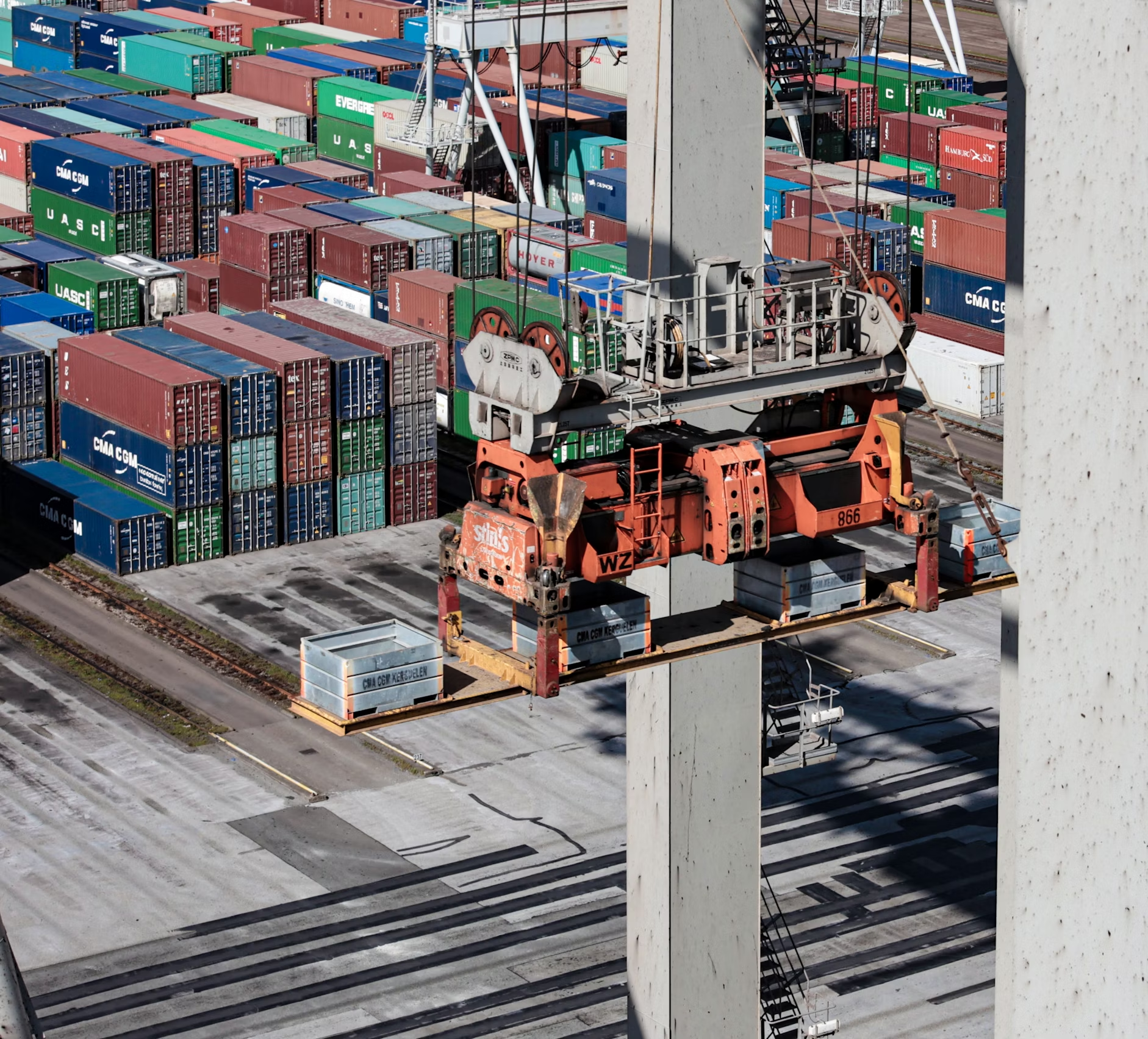
Streamline your shipping procedures, negotiate better prices, and achieve cost-efficient freight management by leveraging technology. Practical and successful solutions are explored in this article. Improving your bottom line and keeping your supply chain strong are both possible with these tactics.
How To Reduce Freight Costs?
Reducing freight costs is crucial for businesses looking to improve their bottom line. Here are several strategies that can help:
Optimize Packaging
- Reduce Package Size: Use the smallest possible packaging without compromising product safety. Smaller packages reduce dimensional weight charges.
- Use Lightweight Materials: Switch to lighter packaging materials to reduce weight-based shipping costs.
Negotiate with Carriers
- Volume Discounts: Negotiate for better rates based on your shipping volume.
- Rate Shopping: Regularly compare rates from different carriers to ensure you are getting the best deal.
- Long-term Contracts: Secure long-term contracts with carriers for better rates.
Leverage Technology
- Freight Management Systems (FMS): Use software to optimize routes, consolidate shipments, and automate processes.
- Tracking Systems: Implement tracking systems to monitor shipments and identify inefficiencies.
Consolidate Shipments
- Combine Shipments: Consolidate multiple smaller shipments into larger ones to benefit from bulk shipping rates.
- Third-Party Logistics (3PL): Use 3PL providers who can consolidate shipments from multiple clients.
Choose the Right Mode of Transportation
- Intermodal Transportation: Combine different modes of transportation (e.g., rail and truck) to reduce costs.
- LTL vs. FTL: Evaluate whether Less-Than-Truckload (LTL) or full-truckload (FTL) shipping is more cost-effective for your needs.
Improve Supply Chain Efficiency
- Inventory Management: Optimize inventory levels to reduce the frequency of shipments.
- Route Optimization: Use route planning software to minimize travel distance and time.
Review and Adjust Shipping Policies
- Shipping Schedules: Ship on off-peak days to take advantage of lower rates.
- Customer Shipping Options: Offer customers multiple shipping options, including slower, less expensive methods.
Utilize Regional Distribution Centers
- Strategic Location: Position distribution centres closer to major markets to reduce shipping distances.
- Cross-Docking: Use cross-docking to minimize storage time and move goods directly from inbound to outbound transportation.
Engage in Reverse Logistics
- Efficient Returns: Streamline your returns process to minimize the cost of reverse logistics.
- Recycle and Reuse: Recycle packaging materials and reuse shipping containers when possible.
Regularly Audit Freight Bills
- Invoice Auditing: Regularly audit freight invoices for errors and overcharges.
- Claims Management: File claims promptly for any shipping errors or damages.
Implementing these strategies can help businesses significantly reduce their freight costs while maintaining efficient and reliable delivery services.
What Is Freight?
When it comes to international trade, the movement of goods and freight are two of the most important factors. Each critical step of the process—packaging, loading, transportation, unloading, and delivery—requires meticulous planning and oversight to guarantee efficient and timely delivery at a reasonable cost.
Considerations including size, weight, and manner of transportation allow for the classification of freight into many kinds. Full truckload (FTL) shipments take up the whole truck, but less-than-truckload (LTL) shipments are usually smaller and mixed with other shipments.
When it comes to optimizing routes, tracking shipments, and managing inventories, the logistics of freight transportation can be rather complex and rely on advanced technology and software.
Companies in this sector are under constant pressure to find new ways to improve efficiency and sustainability in the face of mounting environmental concerns, shifting regulations, and unpredictable fuel prices.
When dealing with such intricacies, freight forwarders and third-party logistics providers (3PLs) frequently come in handy, providing knowledge and tools to make shipping easier.
Additionally, the volume of freight has grown substantially due to the rise of e-commerce, necessitating more rapid and adaptable shipping options to satisfy customer expectations.
A result of this change is the expansion of intermodal transportation, which combines the advantages of different modes of transportation—for example, train and truck—to move goods more efficiently and at a lower cost.
Efficient and dependable freight transportation is crucial for promoting economic growth and linking markets across the globe, especially as the global marketplace is always changing.
How Are Freight Costs Treated In Accounting?
Freight costs are an important aspect of accounting, as they directly impact the cost of goods sold (COGS) and overall profitability. Here’s how freight costs are typically treated in accounting:
Freight-in Costs (Inbound Freight)
These are the costs incurred to transport goods purchased from suppliers to your business location.
- Inventory Costing: Freight-in costs are usually included in the cost of inventory. This means they are capitalized and recorded as part of the inventory value on the balance sheet.
- Cost of Goods Sold (COGS): When inventory is sold, these costs are transferred from the inventory account to the COGS account on the income statement. This inclusion helps accurately reflect the total cost of acquiring inventory.
Freight-Out Costs (Outbound Freight)
These are the costs associated with shipping goods to customers.
- Selling Expense: Freight-out costs are generally treated as a selling expense and recorded on the income statement. They are not included in the cost of inventory or COGS.
- Freight Recovery: If you charge customers for shipping, the amount received can be recorded as a revenue item under shipping income or freight recovery, offsetting the freight-out expenses.
Freight Costs For FOB Shipping Point And FOB Destination
- FOB Shipping Point: The buyer is responsible for freight costs. The buyer will include these costs in the inventory value.
- FOB Destination: The seller is responsible for freight costs. The seller will record these as selling expenses.
Accounting Entries For Freight Costs
Freight-in (Buyer)
- When goods are purchased:
- Debit: Inventory (for the cost of goods including freight)
- Credit: Accounts Payable or Cash (for the total payment including freight)
Freight-out (Seller)
- When goods are sold and shipped:
- Debit: Freight-out Expense (for the cost of shipping)
- Credit: Accounts Payable or Cash (for the payment of shipping costs)
Freight Cost Allocation
- Direct Allocation: If freight costs can be directly traced to specific inventory items, they should be allocated accordingly.
- Indirect Allocation: If freight costs are not easily traceable, they can be allocated based on a reasonable method, such as weight, volume, or value of the inventory items.
Impact On Financial Statements
- Balance Sheet: Freight-in costs increase the value of inventory assets.
- Income Statement: Freight-in costs impact COGS, while freight-out costs impact selling expenses. Both affect net income.
Understanding and accurately accounting for freight costs is essential for proper financial reporting and analysis. By correctly treating these costs, businesses can ensure their financial statements reflect the true cost of acquiring and delivering products, aiding in better decision-making and financial management.
Conclusion
Any company that wants to stay profitable and run efficiently must master the art of freight cost management. Businesses can improve their financial reporting and overall health by learning how freight charges are treated in accounting.
Incorporating freight-in costs into inventory value and having them represented in the cost of goods sold is the correct approach, whereas selling expenditures should be used to account for freight-out costs.
Businesses can have a better understanding of their actual spending through accurate cost allocation and accounting, which in turn allows for better strategic planning and decision-making. Businesses can improve their financial standing and ensure their continued growth by adopting industry-leading techniques in freight cost accounting and management.